Lean Change Agent
- By Terrance Campbell
- •
- 12 Jun, 2017
- •
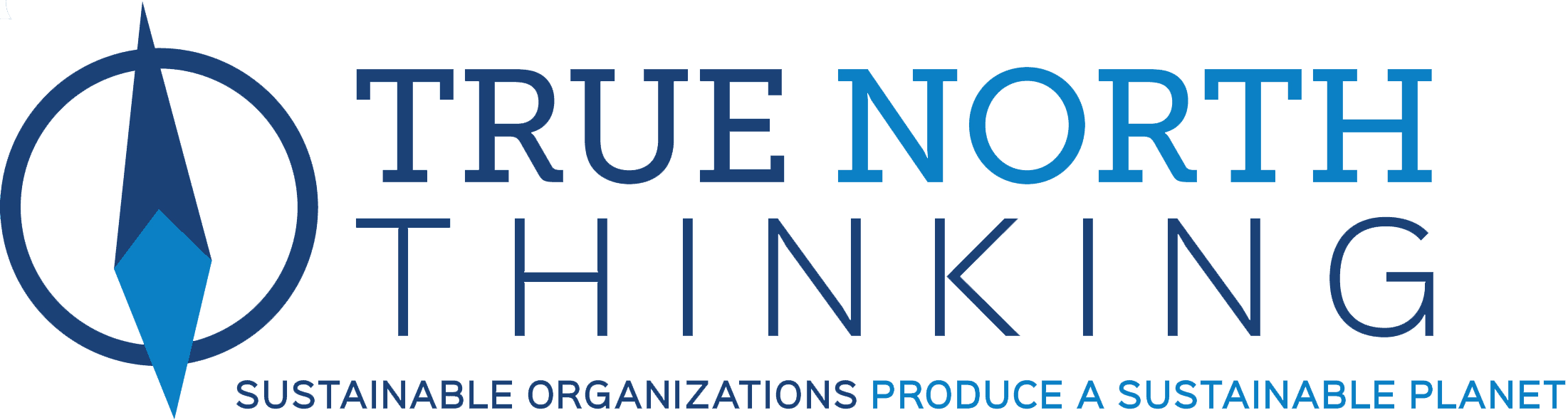
Carol M. Shaw
Professor Emeritus, University of Dayton
True North Thinking, LLC.
In the 30 years I have worked as a change agent, first working in the field of engineering education to change the enrollment patterns of women in engineering, and then as one of the early adopters helping introduce Lean to the United States as a new model of management and finally as a co-teacher with Professor Joseph Castellano, University of Dayton School of Business, as part of a MBA course entitled “The Principles of Deming and Lean and How Metrics Influence Management Outcomes”, sometimes in surprising ways. Because of being a student of Lean as well as establishing a certificate program in the area, I have learned a lot about how Lean management compares to traditional management methods and I thought I would describe those differences as I have discovered them.
1. Is Lean the only successful management methodology or can a traditional management approach or hierarchical approach be successful? YES, there are top down and segmented organizations, to use Rosabeth Moss Kanter’s term, (Harvard School of Business), there are management approaches that are successful. However, the success is often the result of the personality of a leader, or the fact that organizations often make money despite themselves. In a good economy with cash pouring in, in the form of sales of products or tax revenues to support schools, waste or nonvalue added activities from the standpoint of the customer or tax payer parent or the students they represent can be covered up.
Miami University was in a comfy situation in regard to tax revenue to support operations, until 2008, when suddenly they were faced with a $30,000,000 reduction. Miami University needed a proven management system that would reduce cost in operations and they turned to lean, even though it would involve systemic change. Initially they turned to The University of Dayton Center for Competitive Change to help them adopt Lean because of their leadership in this area since the early eighties. Two of Miami University graduates, who formed the Danaher Brothers, were also leaders in the corporate world in adopting lean. In a 2014 article, published to describe the Miami University Lean journey reported a cost savings of $27,000,000 over a period of six years. The savings have occurred by focusing on quality, shifting to process thinking, instituting an organizational approach to reviewing waste in processes and eliminating the waste.
2. What is the difference between Lean and traditional management methodology in terms of waste. Is removing waste really that important? Absolutely. Waste represents unsolved problems in most instances or the “way things work around here”. In a traditional organization, the problems have been ignored for so long that there are “work arounds” built into the system. The Lean methodology offers a different approach than “working around problems”. As the Miami University example illustrates, working around waste is costly and the use of that time could not only be better spent on creative projects, but it is also psychologically exhausting to continually fight the system and work on problems that shouldn’t be there. Given the cost savings of eliminating problems as opposed to working around them, one might ask, why doesn’t everyone shift to lean, why wouldn’t all organizations want to shift to a culture of quality and continuous improvement?
Professor James Womack (MIT), author of Lean Thinking, probably offers the best answer. When interviewing a manager that had worked in a traditional culture versus a Lean culture, the manager related that in the traditional culture he was a “hero” because he was good at working around problems. In fact, he liked “firefighting” and he became the goto person when someone wanted a project completed, he was an expeditor. He excelled at heroic management, was promoted for it and that was all he knew. When finally introduced to working in a Lean culture, all the energy he had been utilizing to conquer the system, was now available for more meaningful work and he says he can never go back. In a culture of improvement, he learned he could use his creativity, introduce products faster and was now able to help his organization compete on the basis of time.
As a final example, the CEO of General Motors, which had the most famous and failed traditional management system, and where people were more or less expected to “work around problems”, stated, “I look at the numbers and they tell me what to do”. This offers a window into the final reason organizations don’t want to shift to lean. Managers like sitting in glass offices, 30,000 feet above from where the work is done and “manage.” This top down approach leads to pleasing the boss or the board as the metric in play, not taking out waste. In fact, in a huge bureaucracy it is not possible to see waste from the glass offices. Instead, in a Lean culture, the management triangle is inverted; Lean is stewardship management in practice.
3. Is there really waste in education, can you provide a specific example of waste in DPS? There are no doubts but you have to be committed to looking for it in a systematic way. A story reported to a DPS Board Member by The former President of Sinclair provides a window into DPS waste. During a July, 2015 luncheon planning meeting with a representative of the DPS School Board and the formative group planning The Dayton Public School Foundation effort., Dr. Ponitz mentioned that the students at the Ponitz School needed computers; he raised $20,000 personally and the school system contributed the rest, approximately $5,000. In recounting the story, Dr. Ponitz was still very upset because as he told the story, he relived the fact that months went by with no computers delivered to students. He finally “attacked the system” to find out why. Eventually the computers were delivered. The point of this story is, it took his heroic effort to “work around the system and make something happen.” And it shouldn’t have!
Regular organizational systems should be able to deliver a product or service on time every time, without heroic intervention. Ignoring problems robs people in organizations of vital energy that could be used to develop new teaching methods, or roll out a new engineering products in a technology-based company. Stated another way, in a traditionally managed organization, creative energy is used to fight the system to get something done and that creative energy is not available to learn and teach new things to students or to contribute to organizational success.
4. Lean has been demonstrated to work in manufacturing, hospitals, dentist offices, law enforcement and education and to save money as a result of removing waste. Why does Lean produce so much additional revenue for organizations and what is meant by the moral or morale reason for adopting lean? Removing nonvalue added activities adds up, e.g. $27,000,000 for Miami University over a six-year period reported In an article for Quality Progress, Feb 2015. How much time is really tied up in wasteful activities? The Lean literature claims that 75% of all work activity is non-value added. This means that we are routinely engaging in activity the customer, parent, tax payer is not willing to pay for. When analyzed this way, huge amounts of time could be freed up or redirected: more time spent with students, more time to find out, what are “the best practices in 3rd grade reading?” From the standpoint of students, this should be a moral dilemma?
Stated another way, the money that is now spent on nonvalue added activities could be invested in our economic and educational future. Consider this example as a project we worked on for a university. It took a University 106 days to buy a computer for faculty. When the process was analyzed, only several hours were actually value added, all of the reviews upon reviews and wait time in somebody’s inbox was nonvalue added. The money that was spent to pay all those people for nonvalue added activity is now freed up and drops to the bottom line. In the university computer example, I don’t think we got the purchase time down to one day, but we reduced it dramatically. After a change like this happens, it is publicized, so the next time a faculty or teacher is frustrated by “the system”, relief set in that there is a process and structure for improvement.
So instead of being demoralized, exhausted, or angry, Lean establishes a mechanism for workforce happiness to set in? Happiness in work, or what we call Work Spirit increases because of the realization that the system includes a structure for self- improvement, improvement that does not depend on any manager’s personality. Analyzing and taking out nonvalue added activities becomes the culture. The subliminal message is, everyone is important enough to submit ideas for improvement. The system no longer feels overwhelming and stagnant but one that has life and one that listens. The listening aspect of Lean is an automatic morale booster.
5. Lean organizations are not only fast, nimble, but their culture is one where the Work Spirit is considered an important aspect of organizational culture. Is Work Spirit really that important to organizational culture?
In the 2012 Gallup Study of the American Workforce, entitled Employee Engagement Insights for US Business Leaders, Gallup reported that only 30% of the workforce was engaged, 20% were actively disengaged and 50% were disengaged. These are startling and hair-raising numbers. We are going to hypothesize that actively disengaged employees do not have or display Work Spirit, or happiness at work, which would mean engagement at work. While the educational workforce was not specifically mentioned, one could hypothesize that the engagement numbers might be worse.
When exploring why large numbers of the workforce are disengaged, one would hypothesize the reason or a contributing factor is that they have no voice in how work gets done. Add to this that many feel they are constantly “fighting the system”, and it takes heroic effort to even get simple things done, like buying computers, when you have contributed the money, the natural outcome of those conditions is not Work Spirit, but fatigue and loss of morale. Lean delivers the Work Spirit factor because by definition it engages the entire workforce in looking for waste. Miami University trained 400 employees in a two-day, team leader workshop to educate in Lean and to spread the problem-solving methodology to all components of the University. When adopting any management methodology, it is important to speak with One Voice. Miami University has wisely chosen Lean and has invited everyone to the table of “improvement”.
Definitions:
Work Spirit:
Speak with One Voice:
Knowledge Based Organization:
Waste: